PROJECT.H VOL.1 : YASUHIKO SASAKIVol.1 佐々木 保彦
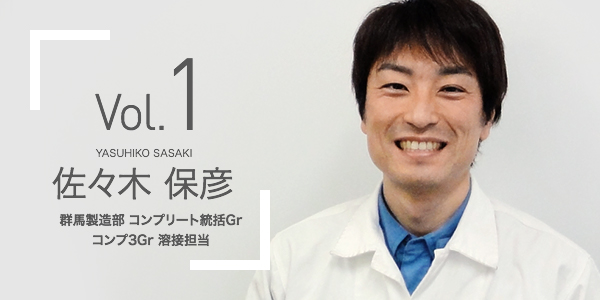
岩手の海沿いの町で育ち、F1を夢見た佐々木。
想いが叶い、レーシング活動に10年携わった。その後、(株)浅野で7年、溶接一筋でキャリアを積む。
「技術の見える化」プロジェクトのF1カーのスケールモデル製作ではフィニッシャーとして
レーシングカーと溶接の経験を結実させる。佐々木の夢を叶えるこだわりのモノづくりを紹介しよう。
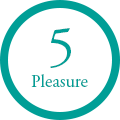
微差を読む
喜びは思い通りの寸法の実現
アルミとカーボンが今回のプロジェクに使われる主要素材だ。この2つ、アルミはF4で、カーボンはF3の車体によく使われる素材だ。アルミの溶接と組立、カーボンとの合わせ工程を担当する佐々木にとっては昔から馴染みのある素材でもある。
ただ今回は1メートルを超えるサイズで、モノコック周辺は溶接箇所も多い。半量産型バイクであれば治具で回転させることで、いいポジションで仕事ができるが、不利な体勢での仕事を余儀なくされる。
まず寸法出しで溶接順序や治具の順番といった重要なポイントを押さえていく。溶接箇所が縮んでひずみが出るので、その分を考慮してイメージ通りのものが出来るように事前の読みが欠かせない。また夏と冬では気温差でひずみの出方が微妙に異なる。溶接の足し算と引き算が必要な訳だ。経験を積み重ねる中で育まれた勘、レーシングカーの整備で培った仕事の取り組み*5、その持てる力を総動員して寸法出しを実施した。設計にも口を出すことで、思い通りの寸法が出た。この読みがあたるのが楽しいと語る佐々木。このように溶接は後工程ながら、設計も含めて全工程に声をかけて仕事を進めていく影の司令塔のような役割も担う。組み立てる上で強度が足らなければ他の現場にリクエストしながらプロジェクトを進めていった。周囲も手持ちの仕事がありながらもよく佐々木の要望に快く応えていった。
失敗が許されない状況下で、自身の判断で美しく仕上げていった。残るはカーボン製部品との合わせこみだ。
「将来の夢は?」と問うと、駆動系を積んだスケールモデルを何台か製作し、サーキットでレースをしたいとのこと。そう語る佐々木はF1を夢見た中学時代に戻ったようであった。